Rotomolding, often referred to as Custom Rotational Molding, is a very effective manufacturing method applied to generate useless plastic services and products with uniform wall width and superior durability. This technique is widely used across industries including automotive, agriculture, construction, and consumer goods. Its rising popularity is because of the unique advantages it includes when it comes to style flexibility, generation efficiency, and solution performance.
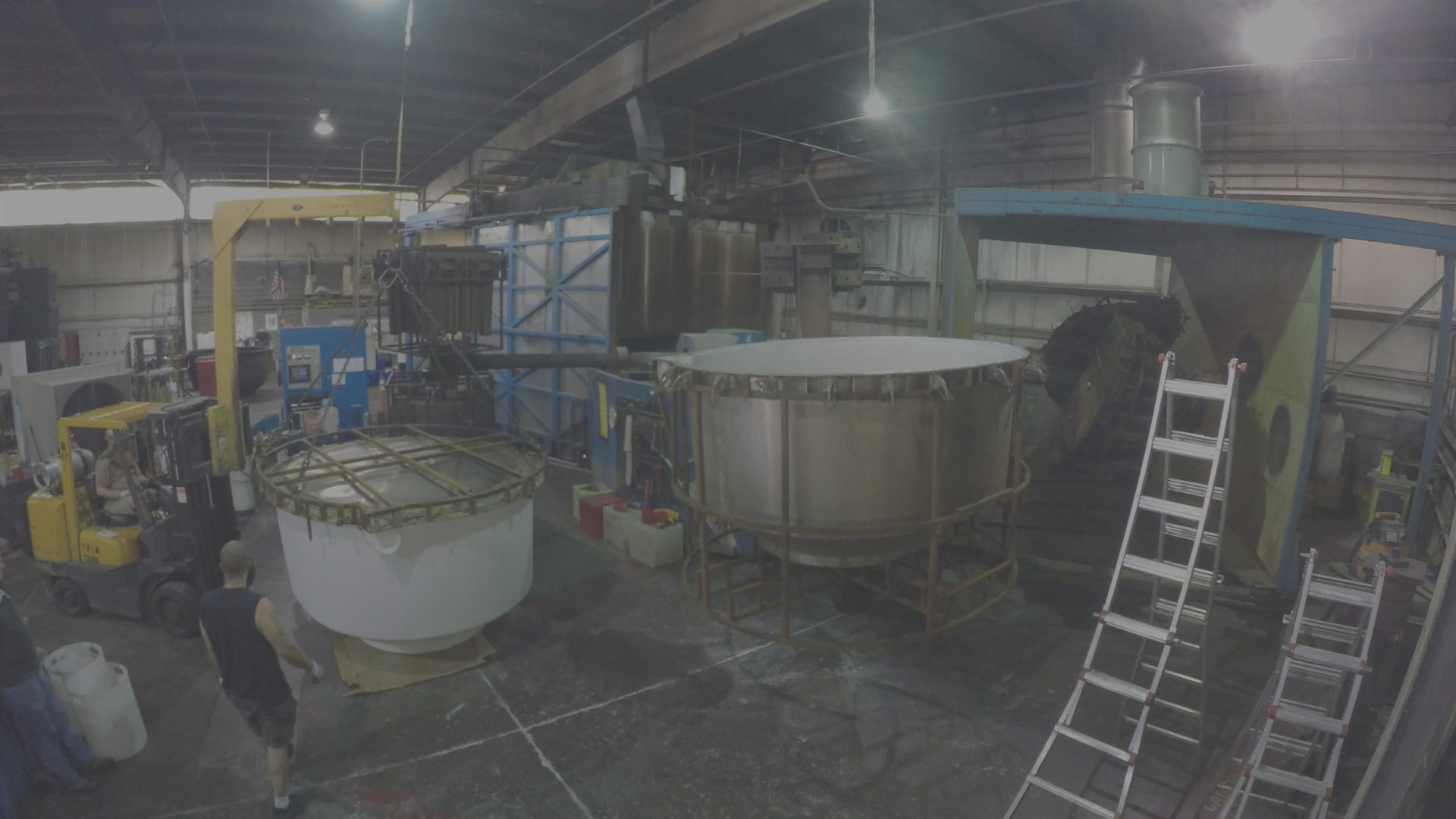
Excellent Design Freedom
One of many standout great things about rotational molding could be the advanced level of style flexibility it provides. Unlike old-fashioned plastic molding strategies, rotomolding enables makers to make complicated shapes, different wall thicknesses, and incorporated features such as for instance handles, posts, and pockets without the need for secondary assembly. This amount of flexibility is great for custom-designed products and services or those requiring delicate detail. The ability to integrate multiple parts right into a simple seamless piece also reduces the necessity for welding or joining parts, increasing both power and aesthetics.
Cost-Effective Tooling and Generation
Rotational molding can also be known for its economical tooling costs. The conforms found in this technique are typically created from aluminum and don't require high-pressure weight, which significantly lowers the original investment. Moreover, the slow, heat-driven means of rotomolding ensures that shapes experience less use and split over time, extending their functionality and maintaining preservation expenses low. That makes the method particularly desirable for short to medium creation goes or market products.
Remarkable Longevity and Architectural Strength
Services and products made through rotational molding are well-known because of their strength and resilience. The strategy guarantees a level distribution of material across all areas, eliminating weak spots and improving affect resistance. Since the pieces are molded as an individual piece, there are no joints or joints that could become details of failure. That makes rotationally carved items perfect for tough conditions, outside use, and heavy-duty applications wherever consistency is essential.
Reliability and Quality Control
Rotational molding provides consistent results across manufacturing batches. Since the plastic-type material is evenly spread throughout the rotation process, the end products and services keep standard wall width and architectural stability. That uniformity contributes to reliable efficiency and expected outcomes, which are important in industries that demand strict quality standards.
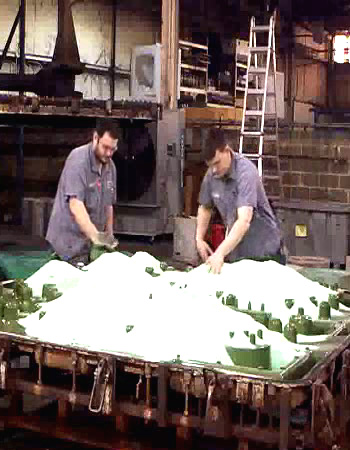
Environmentally Friendly and Low-Waste
From the sustainability perception, rotational molding is really a low-waste process. Surplus material from the shape can often be reused, and the procedure it self doesn't count on harmful compounds or produce substantial emissions. More over, the effectiveness of producing single-piece products reduces the necessity for extra products or power for assembly. Several companies will also be shifting toward using recyclable or biodegradable plastics inside their rotomolding procedures, further improving environmentally friendly benefits.
Conclusion
Rotational molding presents a combination of affordability, design usefulness, durability, and environmental effectiveness that few other manufacturing techniques may match. Whether producing little parts or big, tough bins, this approach continues to demonstrate it self as a dependable option across various sectors. For producers seeking top quality, custom plastic parts with little spend and long-term value, rotational molding stays a top-tier choice.